Carbon Graphite Inner Inlet Barrel
The world’s ONLY permanent solution to the unavoidable corrosion problems plaguing newer generation inlet cowl Inner Barrels.
The QTA inlet Upgrade Program replaces and terminates the corroding Aluminum Inner Barrel with a state-of-the-art, one piece, Carbon Graphite Composite Barrel that will never fail.
STC approvals around the globe.
A Problem that Doesn’t Get Better with Age
Growing fleetwide & expensive problem of corrosion that began on the drawing board.
- Higher performing jet engines demanded quieter operation
- To be quieter, acoustic elements to the inner barrel were added
- The added acoustic screen traps moisture
- Moisture induces inner barrel corrosion
Not only is a repair unavoidable and expensive, corroded metal dislodged and feeding through the engine is a very serious safety concern.
To provide increased efficiency and lower noise levels aircraft turbo fan engines have been increasing their Bypass ratio for many years; the ratio of thrust generated by the Fan vs the Jet Core has increased incrementally from 2:1 to as high as 10:1.
To achieve these higher Bypass ratios the diameter of the engine fan has increased. One negative side effect of this is increased forward radiated fan noise that impacts both cabin and ground noise levels.
There is a generation of aircraft where the need for increased acoustic sound suppression in the inlet was achieved through adding an ‘Acoustic’ screen over the traditional aluminum honeycomb panels with open perforated face sheets that make the inner barrel.
The acoustic screen is a permeable fine woven wire mesh and is a powerful acoustic tool.
Unfortunately, in the quest for increased sound attenuation the effect of moisture entrapment in the aluminum inner barrel honeycomb cells was not contemplated. Previous generation inlet cowls with open perforated holes are self-drying, the engine vacuums the moisture out; this does not happen when the acoustic screen is added. This results in moisture being trapped in the cells.
The end result is guaranteed eventual corrosion of the aluminum honeycomb and perforated face sheet.
Once the underlying structure has corrosion the adhesive used to apply the acoustic screen will dis-bond and the acoustic screen will bubble up and detach.
The Solution Starts and Ends with QTA
Decades of applied QTA ‘game-changer’ acoustic technology to earlier generation (and much louder) jet engines, combined with state of the art materials technology and engineered manufacturing finds a solution.
- Until QTA, the only option was to replace the corroded OEM inner barrel with a new barrel or repair, both use exactly the same material, both are designed to fail again.
- This is not a true solution, rather a band-aid fix. The only guarantee you get is that this barrel will corrode just like the one it’s replacing.
- OEM engineered aluminum inner barrels are 100% guaranteed to fail, it’s inevitable.
In attendance at an operators conference by QTA, a specific workshop/briefing was ‘Update on Inlet Cowl Corrosion’.
It was apparent to QTA that once an inlet’s inner barrel has corrosion there is no way to remove it.
The corrosion starts inside the Honeycomb cells and works its way out. Repairs were failing within 3-4 years and replacing the inner barrel with the same item and same materials, guaranteed only one result, it will corrode and fail again.
QTA has nearly 40 years of experience with composites and acoustic technology, originally for Hush Kits.
QTA engineers and management concluded the ONLY solution for operators was to eliminate the root cause of the corrosion and provide a PERMANENT solution.
The Carbon Fiber Composite Inner Barrel
STC’s approved worldwide
An upgrade decision to the QTA Carbon Fiber Inner Barrels is the easiest decision you’ll ever have to make.
- Lifetime fully transferable warranty
- Substantial weight savings
- Far lower cost than flawed OEM inlet
- Quick turn time
- Exchange program minimizes downtime
- Robust manufacturing quality that is higher than the OEM
Replacing the original aluminum inner barrel with a one-piece barrel made from Carbon Fiber that will never corrode.
Construction uses Carbon Fiber for the inner and outer skins with a Nomex honeycomb core. Impervious to water, salt, oils, jet fuel, anti-ice fluids, detergents, acid rain, about anything imageable that can get in an Inlet.
Providing the same or better noise attenuation, lighter in weight and extreme durability ensures a lifetime of trouble free, reliable service.
With over 290+ Carbon Fiber Composite Inner Barrels in service on eight affected aircraft models, our results speak for itself.
Lifetime Structural Warranty
Lifetime means Lifetime
An upgraded QTA Permanent Solution Carbon Graphite INLET BARREL and ACOUSTIC SCREEN are backed by a lifetime structural warranty, assigned to the aircraft’s serial number and fully transferable.
- Backed by Product Liability Insurance formed and placed by Lloyd’s of
London. You’re covered – For Life - A QTA warranty remains with the aircraft serial number and is automatically transferable throughout the airplane’s life

Exchange Program
QTA offers a low-cost inlet ‘exchange program’
- Keeps your aircraft free from extended AOG downtime
- Provides either exchange inlets or upgrade a complete set of inlet cowls in two-three weeks
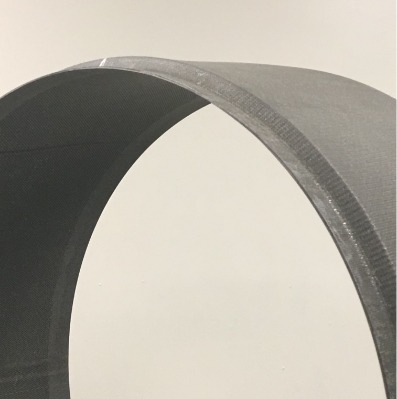
In Service Around the World
Over 290 inlets installed and in service. Available for:
- Bombardier Challenger 300 and 350
- Bombardier Learjet 60 and 60XR
- Dassault Falcon 2000EX/LX
- Gulfstream G200, G280 & G450
- Hawker 1000
- Embraer Legacy 450/500 series and Embraer Praetor 500/600
- Textron Longitude 700
Compatibility, Application & STC Approvals
CHALLENGER 300/350 | HTF7000 | WBA7160E101-041 | ST04417AT | 10065518 | SA18-98 | 2018SS11-03 | IA-587-2019 |
WBA7160E101-045 | |||||||
WBA7160E101-049 | |||||||
WBA7160E101-051 | |||||||
WBA7160E101-053 | |||||||
QTA | CH3-NC-6300-101 | ||||||
EMBRAER 450/500 & PRAETOR 500/600 | HTF7000 | WBE7160E101-045 | ST04464AT | 10077612 | Applied For | Applied For | IA-783-2021 |
QTA | CH3-NC-6300-101 | ||||||
FALCON 2000 DX | EASy | EX | LX | LXS | S | PW308C | 06ND71600-1 |
06ND71600-3 | |||||||
QTA | F20-NC-2000-101 | ||||||
GULFSTREAM G200 | PW305 | LH 288-0101-501 | ST04261AT | 10065841 | Approved | 2017S03-09 | IA-588-2019 |
LH 288-0101-505 | |||||||
LH 282-0211-505 | |||||||
QTA | LH G20-NC-6200-101 | ||||||
PW305 | RH 288-0101-504 | ||||||
RH 288-0101-507 | |||||||
RH 282-0211-507 | |||||||
QTA | RH G20-NC-6200-103 | ||||||
GULFSTREAM G280 | HTF7000 | WBD7160E101-041 | ST04444AT | 10070475 | Approved | Applied For | IA-636-2019 |
WBD7160E101-043 | |||||||
WBD7160E101-045 | |||||||
WBD7160E101-053 | |||||||
QTA | CH3-NC-6300-101 | ||||||
GULFSTREAM 450 | RR Tay Mk 611-8C | LH 1159P41150-9 | STC ST04522AT | 10077605 | Applied For | Applied For | IA-784/2021 |
LH 1159P41150-41 | |||||||
QTA | G45-NC-6400-101 | ||||||
RH 1159P41150-21 | |||||||
RH 1159P41150-43 | |||||||
QTA | G45-NC-6400-103 | ||||||
HAWKER 1000 | PW305 | LH 266-0101-501 | ST04265AT | 10073535 | NA | NA | IA-708-2020 |
LH 266-0101-507 | |||||||
LH 266-0101-511 | |||||||
LH 266-0101-515 | |||||||
QTA | LH H10-NC-6100-101 | ||||||
PW305 | RH 266-0101-503 | ||||||
RH 266-0101-509 | |||||||
RH 266-0101-513 | |||||||
RH 266-0101-517 | |||||||
QTA | RH H10-NC-6100-103 | ||||||
LEARJET 60/60XR | PW305 | LH 282-0211-501 | ST04233AT | 10065432 | Approved | 2018S11-01 | IA-585-2019 |
LH 282-0211-505 | |||||||
QTA | L60-NC-6000-101 | ||||||
RH 282-0211-503 | |||||||
RH 282-0211-507 | |||||||
QTA | L60-NC=6000-103 | ||||||
TEXTRON LONGITUDE 700 | HTF7000 | ST11856AT |