Quiet Technology Aerospace (QTA) is a market leader in the application of advanced composites for noise attenuation and structures.
QTA is located in Hollywood, Florida and the company holds FAA approvals for PMA (Parts Manufacturing Approval) and Part 145 Repair Station. QTA operates from a 30,000 sq ft air conditioned facility with a 2,000 sq ft clean room, two certified paint booths, curing ovens, refrigerated storage, materials test laboratory and associated equipment required to support both new production and repair services.
Since 1988, our Companies have achieved 11 Supplemental Type Certificates (STC’s) for Hush Kits on large transport aircraft, military transports and corporate business aircraft.
STAGE 2
- Douglas DC8-51
- Douglas DC8-61
- Boeing 707-100
- Boeing 707 300
STAGE 3
- Douglas DC8-51
- Douglas DC8-61
- OC135B USAF Special Ops
- Aer Macchi MB339
- BAC 1-11 400
- Gulfstream GII/GIIB/GIII
- Gulfstream QTA Plus GII/GIIB/GIII
QTA first introduced Carbon Graphite Composites on the DC8 hush kit certified in 1988, that’s 35 years of in service experience with advanced composites. The use of advanced carbon graphite was applied to Inlet Cowl inner barrels, Inlet Bullets, By-pass fan ducts and ejectors, as well as structural components used in the installation of the hush kits.
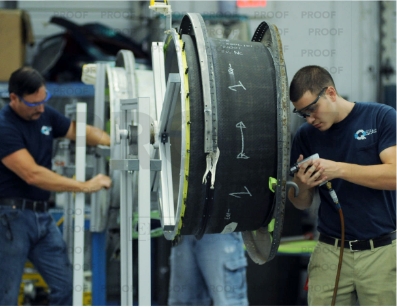
Our Legacy
As the leader in Hush Kit design and manufacturing, QTA established a unique combination of skills and capabilities:
- FAA approved material and process specifications for composite structures that have been used on multiple programs.
- Suppression of engine noise utilizing advanced acoustic solutions.
- Thrust Reverser and Systems design, modification and overhaul.
- Structural and systems detailed design and substantiation.
- FAA and overseas certification of products through the STC process.
- Cost effective manufacture of composite structures combining optimized acoustic treatment.
- Product support and repair services for Composite Structures and Thrust Reversers.
The last of our legacy products is the Stage 3 Hush Kit for the Gulfstream GII, GIISP, GIIB, and GIII, in 2003 and QTA has delivered over 125 aircraft sets.
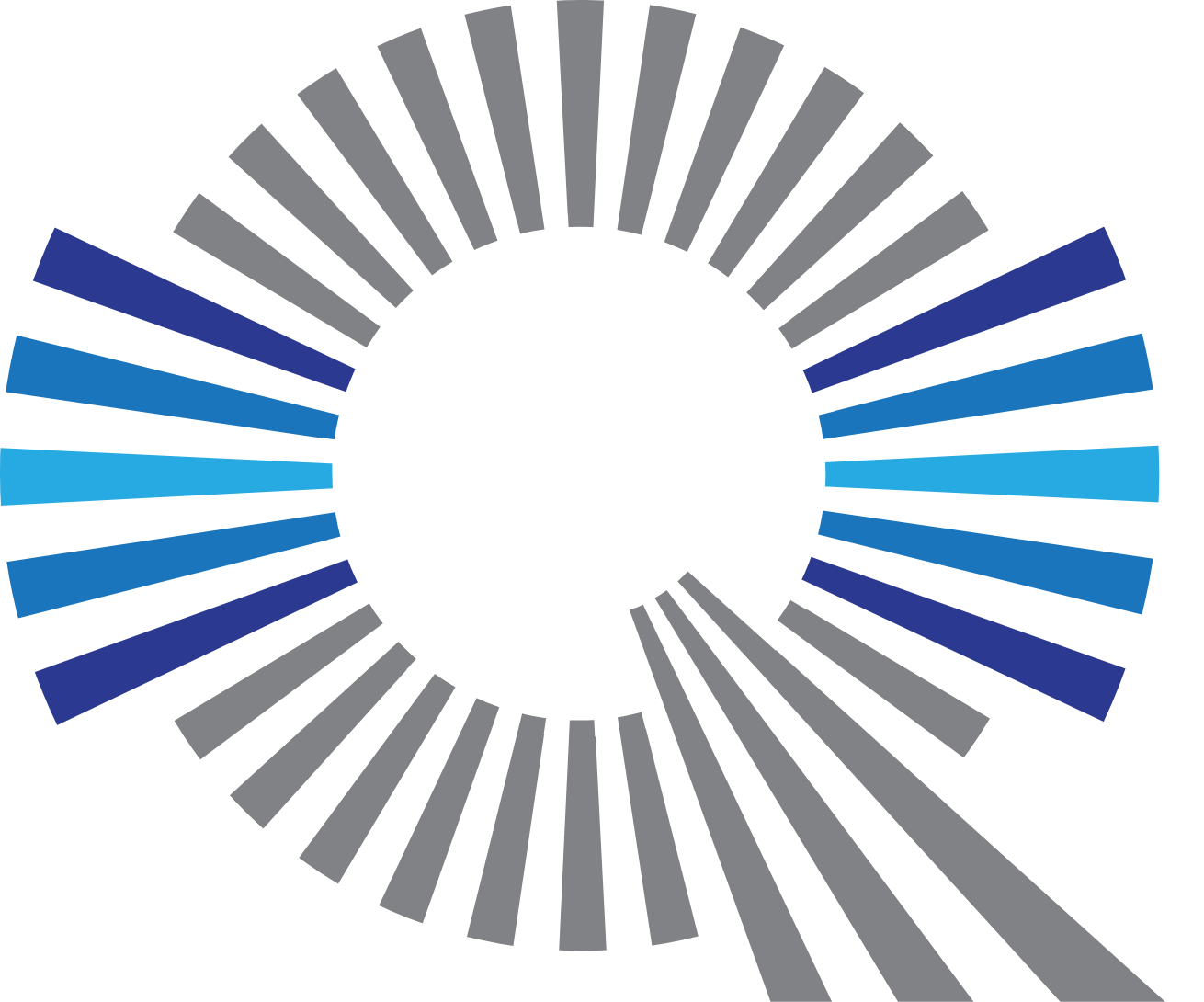
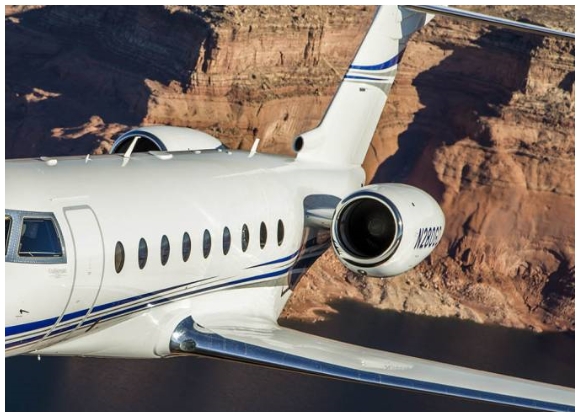
Presently, we are...
Solving in-service corrosion problems to relieve operators from the cost and down time associated with unserviceable nacelles with corroded Inlet Cowls and Thrust Reversers.
Inlet Cowls
Our core skills of advanced composite materials technology and acoustic engineering has been applied to solve in service corrosion issues with Inlet Cowls, replacing the original OEM aluminum honeycomb inner barrel that corrode with an advanced composite unit that will last the life of the aircraft. The first of these for the Lear 60 aircraft was awarded its STC in October 2015, since this milestone a further 7 Inlet STC’s have been awarded.
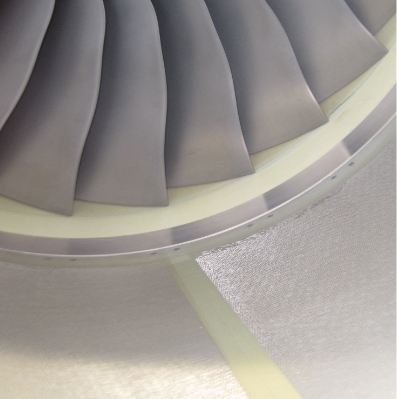
Inlet Upgrades Certified
Lear 60/60XR
Gulfstream G200
Hawker 1000
Falcon 2000EX/LX
Challenger 300/350
Gulfstream G280
Embraer Legacy 450/500 and Praetor 500/600
Gulfstream G450
Textron Longitude 700
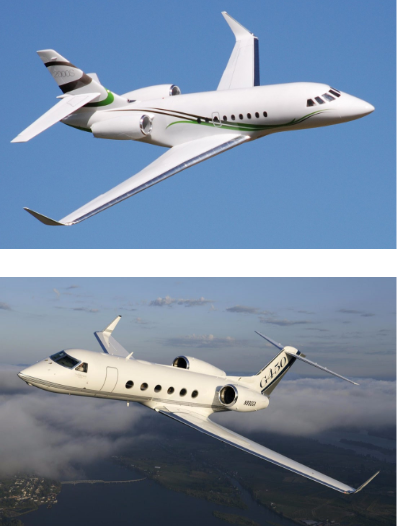
Thrust Reversers
Our involvement in providing Inlet Cowl upgrades for the HTF7000 powered aircraft, CL300, G280, Legacy 450/500, resulted in many operators asking if QTA could solve the Thrust Reverser corrosion problems that were considered more severe and certainly more expensive than the Inlet cowls. QTA investigated this, identified the root cause and the solution. The full scale engineering program was launched in August 2020to deliver the HTF7000 Thrust Reverser Upgrade, a permanent solution that will have the companies unique Lifetime Warranty.
FAA Project Number ST16729AT-T has been issued and the program is on schedule to achieve certification ii the first quarter 2022.
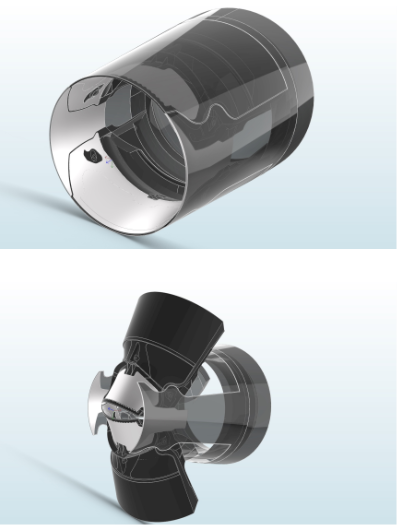
In Service Support
In Service support, our FAA approved 145 Repair Station #Q9TR440N provides support for composite and structural repairs as well as thrust reversers on Gulfstream GIII, GIV, GV, G450, G550, Lear 35, 36, 60 series, Hawker 125/1000, IAI Westwind and Galaxy and Bombardier Challenger 300/350. QTA has in house engineering to develop bespoke repair solutions aimed at providing operators best value, and time savings.
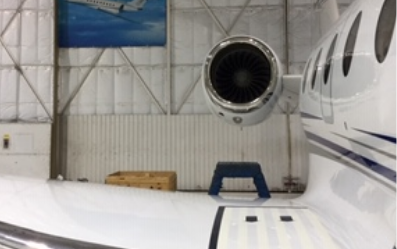
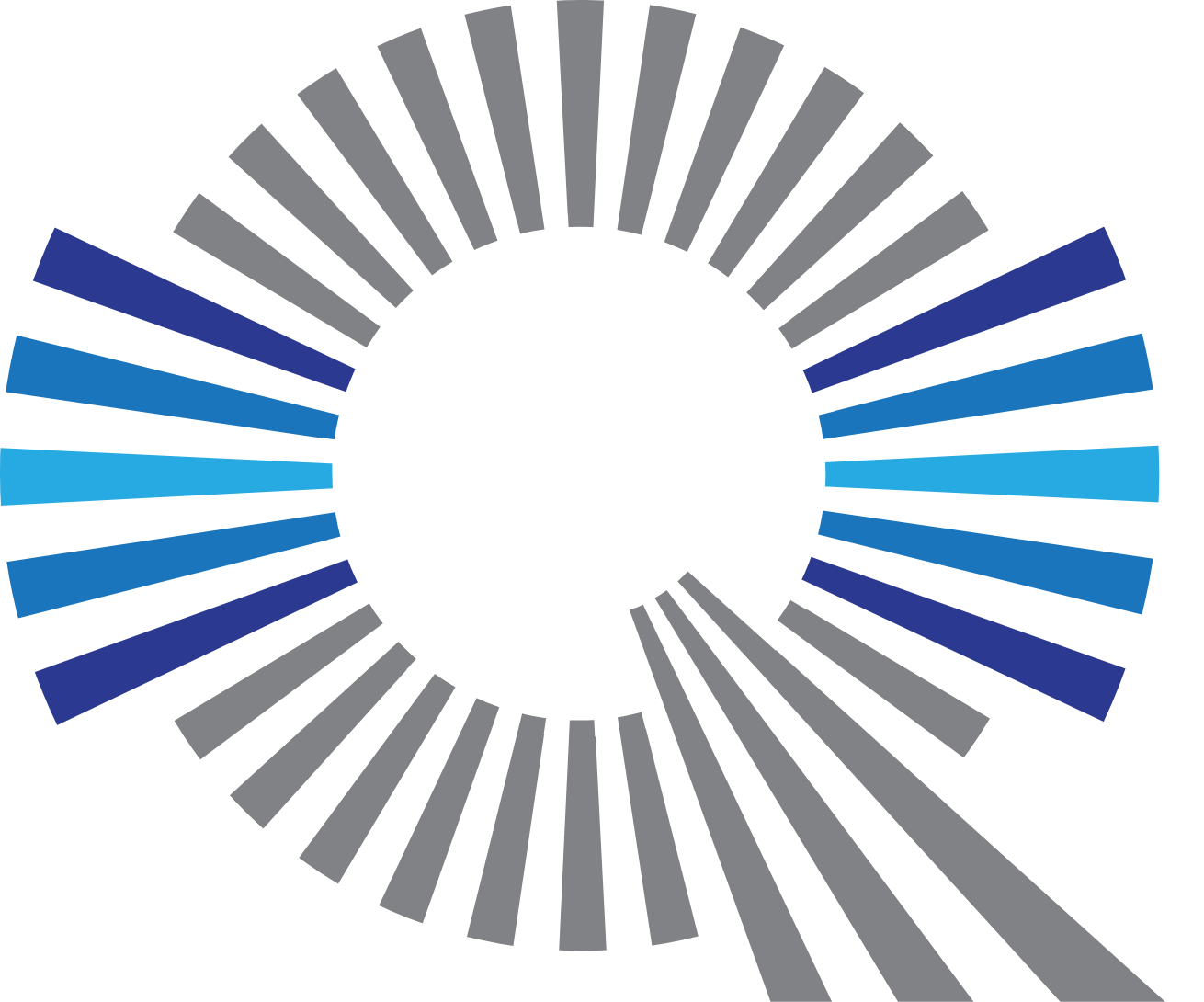
Meet the Team
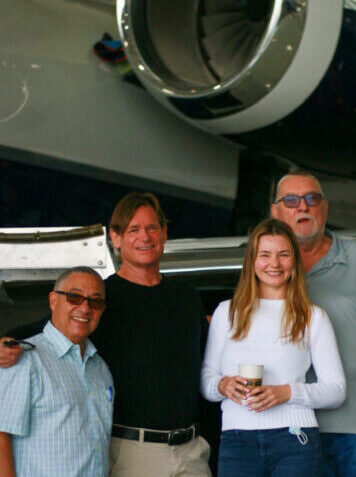
Faustino Dominguez
Q.C. Manager DMIR
305.687.9808 x213
Faustino@QTAerospace.com
Barry H. Fine
CEO
305.687.9808 x202
cell. 305.282.8005
bfine@qtaerospace.com
Irina Dudina
Customer Support Manager
305.687.9808 x213
irinad@qtaerospace.com
Martin K Gardner
Executive Vice President Engineering
and Customer Support
305.687.9808 x216
cell. 954.292.2774
martinkg@qtaerospace.com
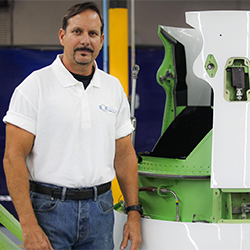
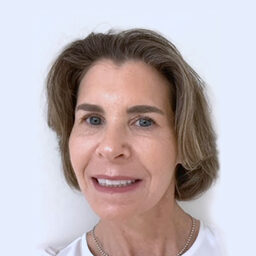
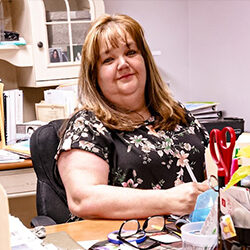
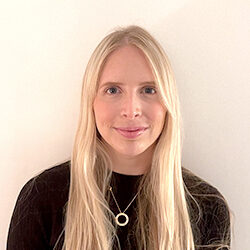
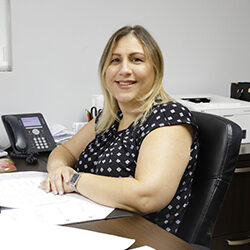
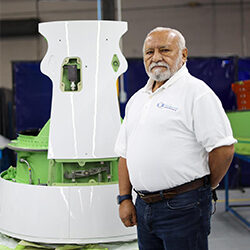